As a tool supplier to the global aerospace manufacturing industry, Iskar continues to develop to ensure more efficient and cost-effective cutting tools for a wide range of machining needs. In addition to its success in other areas, Iska enjoys a good reputation for providing innovative and efficient solutions to the overall leaf disc.
The integral leaf disc is a single aero engine assembly consisting of one wheel and multiple blades. The purpose of developing an integral leaf disc is to replace the traditional fabricated leaf disc consisting of a wheel and a plurality of removable vanes. Since the introduction of the market in the mid-1980s, the overall leaf disk has become more and more popular in the market. Whole leaf discs, also known as integral leaf disc rotors (IBR's), are often machined from monolithic materials.
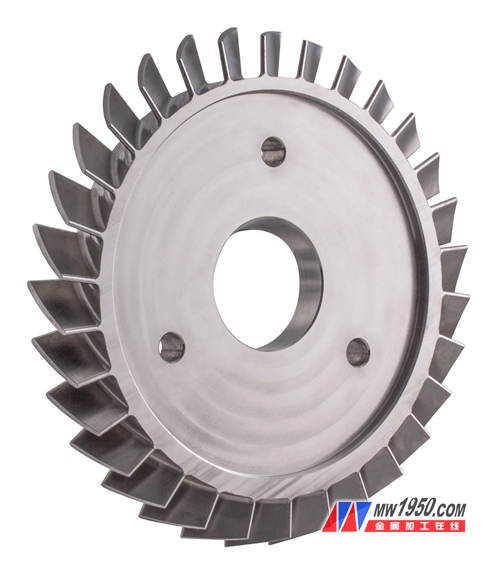
The use of modern turbojets in the overall blade compressor not only results in improved performance, but also eliminates the assembly of the discs and blades and enables important components to be machined on the same machine in a single setup. .
Due to the complex shape of the whole leaf disc, the machining of the parts requires the use of multi-axis machine tools and cutting-edge CNC software, as well as efficient and reliable cutting tools. Since the main machining method of the overall blade is milling, the quality of the milling cutter is of paramount importance. The integral leaf disc is usually made of titanium alloy (Ti) or nickel-based alloy (Ni), so the milling cutter used needs to meet the demanding productivity and the neat processing requirements of such difficult-to-machine materials.
As one of the leading suppliers of aerospace manufacturing in the world, Iskar has developed a number of long-life, high-performance milling cutters that not only help to ensure the high quality of the overall leaf disc, but also significantly increase user productivity. Iska's answer to the efficient processing of the overall leaf disc is to provide a solid carbide end mill with the company's high-quality coating technology and a technologically innovative transformer-type end mill (MULTI-MASTER).
The relevant tools are from the research and development department of Iskardo. Iskar's use of sub-fine grain and ultra-fine grain matrix combined with PVD nano-coating technology and leading edge beam coating post-treatment technology (SUMO TEC) significantly improves the impact strength and wear resistance of the tool. Increases tool life and improves machining characteristics.
The milling process originating from the integral blade disc starts with the roughing of the groove. Iska developed the solid carbide end mill ECK-M for this machining requirement. The cutting edges of these high-efficiency milling cutters are specially treated to have a strong geometry and are ideal for efficient milling of titanium alloys.
The Transformer End Mill (MULTI-MASTER) consists of a shank and a cutter head. The interchangeable carbide tip is threaded to the shank for quick change of the cutter head. The advantages of the flexible Transformer End Mill System, in addition to minimizing the clamping time, also the ability to assemble standard shanks and cutter heads into more than 15,000 combinations. Extension rods can also be used in the assembly if necessary. Whether it is a steel shank for conventional machining tasks or a high-rigidity carbide shank or a tungsten alloy shank with vibration resistance, Iskar offers a range of shanks that greatly increase assembly options.
In the case of groove milling roughing of some whole leaf discs, such as machining nickel-based alloys, cycloidal machining is a very efficient machining method, so the cycloidal tool path is highly recommended. The Iskar anti-vibration and noise reduction end mill (CHATTERFREE) EC-H7 is specially made for this type of processing. The milling cutter has seven cutting edges with unequal helix angles to achieve high metal removal rates.
High finish surface finish and predictable long tool life are critical when finishing the entire leaf disc. End mills often use a large overhang to finish the milling process, which has a high demand for the machining stability of the tool. For such processing conditions, ISK recommends the use of a cone-necked anti-vibration and noise-reducing solid carbide ball end mill (CHATTERFREE), which has the characteristics of unequal helix angles. In addition, in many cases, the use of a tapered neck ball end mill (MULTI-MASTER) cutter head provides an acceptable, more economical solution.
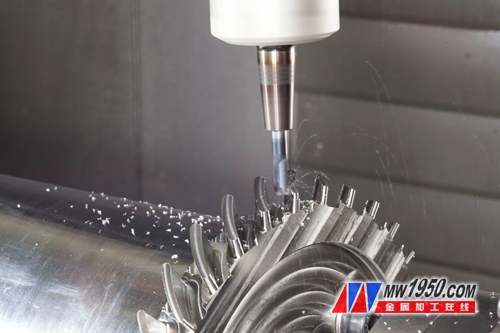
The efficient milling of the integral leaf disc is based on three pillars: a high-speed multi-spindle machine, an advanced CNC system and CAD/CAM software, and an indispensable high-efficiency milling cutter. Iskar has developed a series of highly efficient cutting tools with new alloy grades and technologically innovative geometries, enabling manufacturers of jet engine blades and integrated leaf discs (IBR) from around the world to significantly reduce the cost per piece of production. (CPU).
Solar Flood Light,Solar Led Flood Lights,Solar Powered Flood Lights,Solar Powered Security Lights
Guangdong Smart Street Lighting Co., Ltd , https://www.gdfldlight.com