Figure 1 shows the forged piece of the 31316/02 from a straight design to a contoured shape with a contoured cone angle of about 30. If such products are formed and expanded, the flow line of the raceway is close to the finished product, which not only improves the material utilization rate, but also effectively improves the contact fatigue strength of the bearing.
1. Process plan determination and difficult analysis
(1) Drawing the forgings Figure 31316/02 The tolerances refer to the current standard, the outer diameter is 2.8+1.2+0, and the inner diameter is 3-0--1.5. To compensate for the possible end defects, the height is appropriately enlarged. 3.5+1.2+0, as shown in Figure 2.
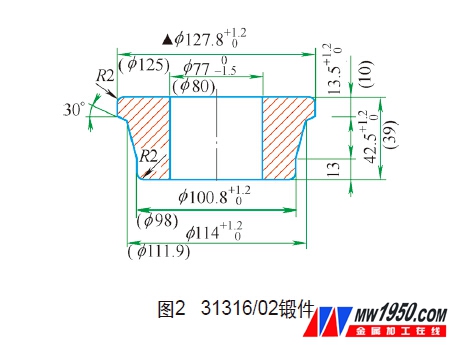
(2) Analysis of processing difficulties During the expansion process, the rolling wheel expands the ring blank with pressure F under the action of the liquid pressure of the D51Y-250E reaming machine. The forgings are relatively thick and long in the radial direction, the metal flows in the circumferential direction, and the inner and outer diameters simultaneously expand. The outer tapered toe has an axial cross-sectional area that is different, and a component force is generated at the slope, so that the local deformation force is reduced and the deformation is difficult. As shown in Fig. 3, the deformation component of the slope from the rolling wheel causes the billet to be thinned, and the other component has a tendency to move the billet toward the small end face (where α is the taper angle of the outer taper forging).
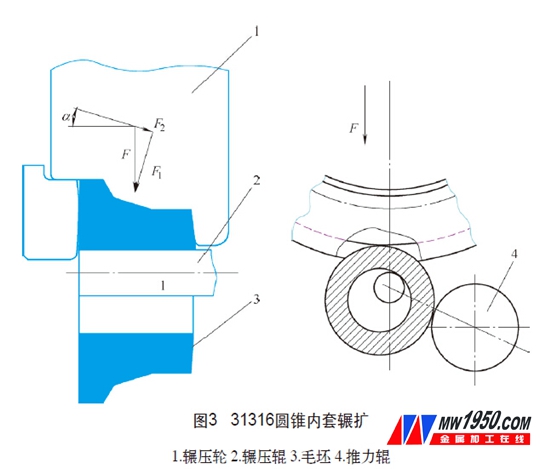
The larger α, the smaller the F1 and the more difficult the deformation. The ability of the reaming machine to distribute metal there is weakened, so it is necessary to ensure that the cross-sections are reasonable when making the blank. The wall of the small end face is the thinnest, the most easily plastically deformed, and the axial burr occurs with the expansion. The wall of the large end face is the thickest, and the surface deformation caused by the expansion force is not easily transmitted to the center of the blank, and the concave core is easily formed.
(3) The process route is determined as shown in Fig. 4. In order to ensure the size of the forging, the inner diameter taper is corrected, and the full diameter step is added after the hole is expanded.
2. Solution
(1) The process key point process guarantees the expansion ratio of 1.3~1.8, and under the premise of ensuring the strength of the pressure roller, the expansion ratio is appropriately increased, and the f 45mm standard punch is selected.
The forging temperature is controlled to prevent over-temperature, and the blank is not allowed to stay at room temperature for too long, and the enthalpy is expanded between 800 and 1100 ° C in the optimum plastic deformation temperature region.
To ensure the performance requirements of the equipment, it is not allowed to excessively move the rolling wheel and the thrust roller to cause the rib size to be out of tolerance (see Figure 5).
(2) Mold preparation According to the law of equal section, calculate the blank size of each section of the forging, complete the “first†dosing of the forging, and focus on the control of the “back-squeeze†of the blank quality, design the semi-closed forming die, and the blank is mostly In the die, the upper part of the large rib is freely deformed. The end face is flattened, and the lower surface is processed into a slope shape (generally 3°~5°), so that the final blank shape is as shown in Fig. 6. When the ram is expanded, the blank is gradually filled with the pressing wheel cavity, which effectively prevents the concave end of the end surface.
3. Production effect
As shown in Figure 7, after the trial production, the 31316/02 forging blanks and finished product dimensions and technical requirements are in line with the process and the appearance quality is good.
Our unit has another 9278, 31316X2/02 two-piece large cone angle forgings put into production. The relevant numerical statistics are shown in the attached table.
It can be seen from the above table that from December 2012 to October 2013, a total of three models were produced, and the material saving rate was over 30%. A total of 6.2 tons of bearing steel was saved, and the economic benefits were remarkable.
About the author: Liu Zhenwei, Wang Yujie, Wang Zhanye, Luoyang LYC Bearing Co., Ltd. Forging Factory.
LED Grow Light
Advantages of led Grow Light:
-
Energy saving. LED grow lamp is efficient light only consume less energy put output powerful light. Environment friendly and saving bill.
-
Long lifespam. LED is durable and with long life 50,000 hours. Which also ensure you lower maintenance cost. Traditional HPS MH grow lights is very easy to fail and almost need to change each year.
-
Better for plants growth. LED grow lights are usually with full spectrum, Plants can use nearly all the light emitted from led grow lights. But usually only 35% of light generated by MH HPS is useful for plants growth.
-
Low heat output. LED grow lights produce very little heat, and they usually with fans or efficient dissipation heat sink. Ensure better growing environment to plants. Traditional lights usually delivery lots of heat. It's very hard for plants especially in summer.
-
Full spectrum. Ideal for all stages of plants growth, from seedlings to flowering to harvets.
-
No worry about dark and terrible weather. You plants can be under light all the time if you open the light all the time. Growing withought resting.
-
Shorten growing cycle but increase yields quality and quantity.
Available led grow lights.
C Series led grow light: cob 600w 1200w 2000w 3000W LED Grow Light, with advanced cob technology, focusing lighting, ensure high ppfd. And this series led grow lights are with veg bloom switches, you could change spectrum from seeding to flowering. And they are daisy chained. easy to use and install.
G series led grow light: G110w G220w led grow light. This series led grow lights are with compact shape, suitable for small space. But they are powerful with samsung leds and reflector. and it's waterproof.
K series led grow light: K1000 K2000 K4000 led grow light, with dimmer. Freely to adjust lighting intensity according plants needs. when seedling, turn dowm it, when flowering, turn up. And down at night, up at noon. Very convenient. The K4000 with a specially design, it can be fold up. easy to carry and install.
L series led grow light: 700w led grow light is a decent light, foldable and dimmable and you could add controller. 700w powerful led grow light is great for weed. PPE 2.8-3.0 μmol/J. Spider grow light design can delivery uniform light, great for weed growing.
M series led grow light: 240w 320w 400w 600W LED Grow Light. This series led grow light is like L700 with dimmer and foldable. They also with spider design. but it with external driver. So you could put driver out of tent, ensure lower heat and easy to control.
If you want to see more, please contact us for details.
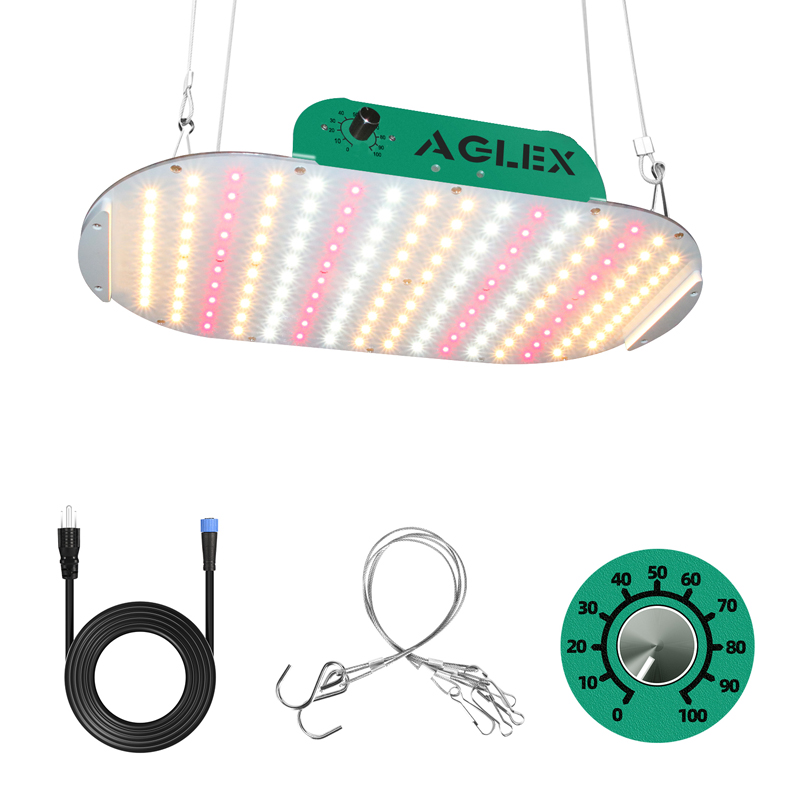
UV Grow Light, Red Grow Light, Orchid Grow Light, Shenzhen Grow Light
Shenzhen Ameri Technology Co., Ltd. , https://www.aglexz.com