Phase transition superplastic effect
The plasticity of metals and alloys increases abnormally during the phase transformation process, and plastic deformation is often produced below the yield strength of the parent phase, which is called phase transformation superplastic effect.
The plasticity exhibited during martensite transformation is much larger than that of superplastic cold austenite. Phase transition superplasticity is a typical case of dynamic superplasticity. The mechanism of plastic deformation is not completely clear. It is generally considered to be carried out by grain boundary slip caused by vacancy diffusion and dislocation motion. The transformation of austenite to martensite is a non-diffusion phase transition process that migrates to an atomic distance. It is extremely fast and undergoes shearing. The specific volume changes the most, causing large internal stresses and residual vacancies. Dislocations are easy to climb, accelerating plastic deformation; the transformation of austenite into pearlite is accomplished by atomic diffusion and redistribution, with a process of nucleation and nucleation growth, speed and specific volume change The martensite transformation is much more moderate. The induced internal stress and residual vacancies are also small, and the acceleration effect on plastic deformation is also reduced; the tissue change occurring during tempering is a solid solution-shedding process with poor effect.
A detailed study of the phase transition superplasticity results in the steel's plasticity increasing by 3 to 20 times in the phase transformation process with the phase deformation, chemical composition and other reasons. During the time of austenite transformation into martensite during quenching, the plasticity increase is most significant, up to 20 times; and when the retained austenite transforms into martensite, the plasticity increases by 10 times; annealing, normalizing The plasticity increase during the transformation of austenite into pearlite is much less, only 3 to 4 times. The plasticity increase during tempering is only 1 to 2 times.
The phase transition superplastic effect is a dynamic phenomenon that occurs during the whole phase transition process, which occurs in the whole process of phase transformation, but in the phase transition temperature range, the plasticity increase is uneven, and the plasticity increase effect is the phase transition. starting time.
2. Application of superplasticity
With its large plastic deformation ability, a small force is applied to the workpiece in the phase transition temperature zone and the phase change time range to make it conform to the required shape, and the purpose of overcoming the deformation is also achieved.
After the application of the phase change superplastic effect, the heat treatment process was improved, and good results were obtained. The deformation problem was solved and some experience was accumulated. The typical artifacts are listed below.
(1) The square hole is shaped to treat a certain hole piece, the material is 30CrNi2MoVA, the hardness requirement is 45~50HRC, and the shape is shown in Fig. 1. The shape of the workpiece is complicated, the wall thickness difference is large, and the square hole is electrolytically processed and used as a follow-up machine plus reference, and the forming is completed once. After quenching, the size and shape of the gage are checked by a combination gage. The thread is S97×5-2, and the thread gauge is used for inspection. The deformation requirements are strict. To this end, the effective martensite austempering scheme is adopted: after heating in a closed box of 880 ° C (adding carburizing agent to prevent decarburization), the air cooling is taken out in a 170 ° C nitrate bath for 40 min. As a result, the shrinkage of the threaded holes and the deflection of the square holes are not satisfactory. Reduce the water content of the nitrate bath to less than 0.5% (the quenched into the workpiece does not boil, do not explode moisture) to reduce the cooling rate, and the threaded hole is qualified. The square hole is still too large (as shown by the dashed line in Figure 1). In order to solve the deformation of the square hole, a limit processing scheme is considered. When the workpiece is cooled and transformed into martensite, a square plunger is inserted to allow the supercooled austenite to undergo a structural transformation under the contact stress of the plunger.
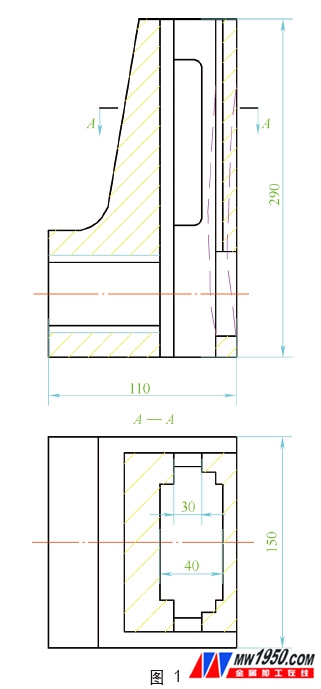
According to the characteristics of phase transformation superplasticity, the martensite begins to transform with the best plasticity. At this time, the effect of inserting the plunger is the best, but the practical operation is difficult: First, the shape of the workpiece is complicated, the thickness is uneven, and the single liquid is used. Quenching and cooling, can not make the same temperature to the same temperature at the same time, there will be intermediate decomposition products in the thick, martensite transformation in the thin part, or even complete, lose superplastic properties; secondly, use martensite point (300 ° C) slightly On the upper temperature quenching treatment, it is difficult to find a suitable cooling rate of the cooling salt bath. Generally, the cooling capacity of the nitrate salt bath to 300 ° C or above is low, the critical point cannot reach the critical cooling rate, and the threaded hole may have a large expansion. Finally, the square hole and the thread use the plunger to limit the shape, the operation becomes complicated, and it is easy to cause interference and cause errors. To this end, we give up the best state to limit the timing, and on the basis of the original martensite austempering, the classification is quenched, and the nitrate temperature bath stays at the medium temperature of 170 °C for 3 min. The workpiece has exceeded the critical cooling rate and cooled to Markov. At the temperature below the body point, the workpiece is taken out and filled into a square hole with a solid square plunger (the size is the lower limit of the square hole size) preheated to about 150 ° C, and air-cooled to room temperature. Some martensite is formed in the classification process, but these martensites have experienced "self-tempering" at higher temperatures, increased toughness, and can accelerate the transformation of austenite in air cooling and reduce austenite. Chen Hua is beneficial and harmless.
After this treatment, the square hole 100% controlled the deformation, no need to make any trimming, and other shapes and sizes are also qualified.
(2) The shaping and quenching guide plate of the guide plate, the material 40CrNiMoA, the hardness requirement is 45 ~ 50HRC, the shape is shown in Figure 2.
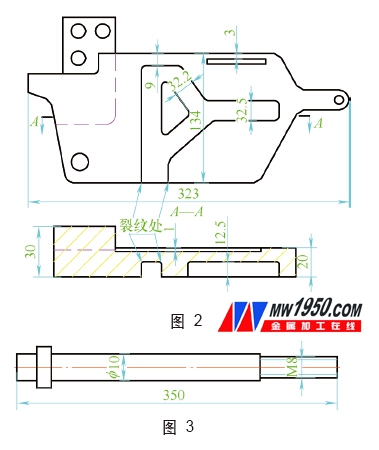
The shape of the piece is complicated, the thickness is uneven, and the grooves are all asymmetrical on one side, and the thickness is from 3 to 5 mm up to 30 mm. After quenching, it is required to have a non-adhesiveness of 0.2mm, and is treated with 170°C nitrate salt martensite. The hardness reaches 53HRC and the plane deflection is 0.3-0.6mm. After deformation, the thermal school often breaks at the cross-section mutation (see the figure). 2).
The reason for the analysis of the deformation is considered to be due to the excessive cross-section of the workpiece and the asymmetry of the shape. Therefore, it has been envisaged to reserve the machining amount (grinding after heat treatment) at the thin wall to reduce the section difference, or to bind the heat balance compensation iron at the thin wall to achieve a more uniform cooling, but in addition to labor and materials, In addition to the cumbersome operation, the asymmetry of the cross-section shape still exists, and the problem is not solved fundamentally. Finally, the plate-shaped quenching is used to overcome the problem of flexural deformation smoothly. The specific method is as follows: firstly make two 40mm thick pressure plates, one for the flat plate, one for the shape of the workpiece to dig a hole, so that the 30mm thick boss falls into the hole, so that the 20mm thick plane can be pressed on both sides; After the workpiece is austenitized at 860 °C, it is transferred to a 180 °C nitrate bath for 1.5 to 2 minutes. The salt is wiped off and placed in a pressure plate. The air is cooled on a 50kN hand press for 10 minutes or more; Because the nitrate salt is not cleaned on the pressure plate, the pressure plate is uneven, which affects the shaping effect. The pressure plate is preheated to 100 ° C before use, and the nitrate salt can be completely solidified without being solidified. After the test, the nitrate salt bath can achieve the cooling capacity above the critical cooling rate under the temperature of 250 °C, so that the hardness is qualified, but the 170-180 °C nitrate salt cooling capacity is large, so it is selected. In the thermal insulation, some martensite is also formed. Although superplasticity is not optimal, the shaping effect can be ensured, and the deflection can be controlled within the range of 0.2mm, without correction. However, the 32.2 mm annular groove shrinks slightly, especially around the middle island-shaped boss. This is because the thickness direction limits the expansion, and the volume change is concentrated to the groove portion. The 32.2mm size tolerance can be solved when the machine is added.
(3) After the spring rod is quenched, the 60Si2MnA spring rod is corrected, and the hardness requirement is 44-50HRC, and the shape is shown in Fig. 3.
The original process is quenching and tempering, and after the stress is removed, the machine is φ10mm outer circle. The piece is an elongated rod, which is greatly flexed after quenching. After tempering, it is just in the elastic range of excellent elasticity, and the straightening is difficult. After changing to quenching, it is not cold-cooled. It is taken out at about 200 °C, and it is corrected during air-cooling to room temperature. At this time, the plasticity is excellent. A little force on the top frame can be used to calibrate, greatly improving efficiency, avoiding school breaks, tempering after aligning and tempering after quenching, saving time and energy. This is based on the 60Si2MnA quenching to about 200 °C martensite transformation is still very incomplete (more than 50% unconverted). Numerous supercooled austenite undergoes martensite transformation during thermal alignment, which greatly increases plasticity.
3. Some views
(1) Apply the phase change superplastic effect to overcome the deformation, and impose constraints on the workpiece during the whole phase change. Too late a constraint and premature constraint will reduce the effect. It is generally considered that it is most effective to restrain the workpiece all the time from the start of the 3% to 5% martensite to the transition amount of more than 90%. To this end, it is necessary to understand the martensite transformation starting point (Ms) and the termination point (Mf) of various steels in order to grasp the timing of the application of the constraint. Figure 4 shows the martensitic transformation temperature range for carbon steel. The alloying elements in steel have a quantitative calculation formula for the martensite transformation starting point Ms, and the termination point Mf can also be qualitatively estimated. The alloying elements that lower the Ms point also lower the Mf point, and the reduction is still slightly Bigger.
(2) Constraining the workpiece in the whole process of phase change can achieve the best effect, but it is often difficult to do. Because the shapes of the workpieces vary widely and vary, the cooling rates vary greatly from place to place, and it is impossible to cool to a certain temperature at the same time and maintain the same state of the organization. Martensite transformation must occur first in the single-liquid quenching thin wall, and the martensite point Ms or higher can be used for the alloying steel with good hardenability or uniform and thin wall thickness. It is effective, and the workpiece with complex shape and wide wall thickness difference, and large deformation, is to be overcome. When it is difficult to restrain the workpiece near the martensite point, the best state is abandoned, and the martensite grade quenching and cooling method is adopted to restrain the workpiece when a large amount of martensite is formed, and at the same time, the deformation is overcome. purpose. The reduction of superplastic properties can be compensated by increasing the binding force, and the increased binding force is still small. If the binding force applied by the guide plate is within 50kN, the unit pressure is about 10MPa, which is much smaller than the supercooled austenite yield strength of 220MPa when it is at the martensite point, but it can effectively overcome the deformation. It is necessary to strictly control the time when the restraining force is removed to prevent new deformation due to premature unloading and subsequent cooling. Generally, it is necessary to cool to room temperature or slightly above room temperature to remove the binding force. In special cases, after the tempering, the retained austenite is rarely or very stable before the restraint is removed.
(3) Using the superplastic effect to overcome the deformation can only change the form of deformation, reduce the degree of deformation, and can not eliminate the deformation of the entire part, and can only choose important size and important shape guarantee. Generally, we only control the reference surface, the difficult surface, the key parts that cannot be corrected or corrected, and the other parts are natural, and other methods are used to make up.
(4) The method of applying the binding force to the workpiece may be various forms such as pulling, pressing, bending and twisting, and may be selected according to specific conditions.
Specifically, for flat plate type, the platen pressure for deflection is used in the form of a mandrel, a sleeve, or the like for deformation such as ellipse and dimensional expansion, and the deformation is overcome by means of contact stress. When the inner hole of the quenched workpiece is required to be hardened, only the cold insert mandrel method can be used. When the workpiece is cooled to a lower temperature, it is inserted into the cold shaft to continue cooling, and after austenitizing, the insert is cooled together. At this time, the mandrel size is the lower limit of the controlled size, and the controlled inner hole of the workpiece is not required to be hardened by the hot plug mandrel method, and the mandrel is inserted into the inner hole to be heated and cooled together, and the operation becomes simple at this time. The circular long mandrel can be inserted into the inner hole together, and the diameter of the mandrel is generally calculated and verified by the following formula:
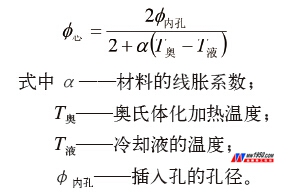
When the cylindrical and pie-shaped workpieces are quenched, the sleeve is used to control the expansion. The workpiece is cooled to the Ms point, and the volume is obviously reduced. It can be conveniently placed in the sleeve (the inner hole is consistent with the outer diameter of the workpiece). The volume of the body transition is swollen and the outer sleeve limits the free deformation of the workpiece to maintain the desired shape and size.
(5) The use of martensite ferromagnetic and austenitic non-ferromagnetic properties can be designed as an electromagnetic chuck type automatic pressure shaping device. When the workpiece is cooled and converted to a certain amount of martensite, the ferromagnet is automatically sucked onto the suction cup. The more the variables are, the harder the suction is, the more the deformation is achieved, the end of the transition, and the suction cup is removed after the power is demagnetized.
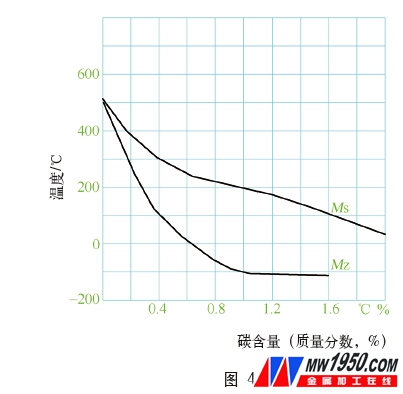
About the author: Zhong Xiangshan, Zhong Liyao, Jiangxi Xinyu Asia Fuji Changlin Elevator (Xinyu) Co., Ltd., Technical Department.
Jiangmen Duramp Electric Co., Ltd , https://www.durampled.com