Abstract Composite materials used in the automotive industry began in 1953. In recent years, composite materials have maintained a growing momentum in the automotive industry, and this trend will continue to move upwards. The amount of composite materials will continue to increase in the automotive industry...
The application of composite materials in the automotive industry began in 1953. In recent years, composite materials have maintained a growing momentum in the automotive industry, and this trend will continue to move upwards. The amount of composite materials continues to grow in the automotive industry because of the many outstanding properties of composite materials such as high strength, light weight, corrosion resistance, and lower processing costs compared to aluminum and steel. The design is more flexible, easier to shape, and more. In short, composite materials are a good alternative to the automotive industry's alternative to metallic materials. However, in fact, in the field of automobile manufacturing, the materials are not completely converted from metal materials to composite materials. Especially in the mass production of automobiles, the application of composite materials is still limited because there are many and composite materials. The use of related technical issues is still not well addressed, including accurate material qualification, production, painting, repair, and joining and recycling of metal materials. Despite the emergence of new materials, new processes and new technologies for composite materials in the world in recent years, the above problems have been greatly improved, which has promoted the wide application of composite materials in various types of automobiles, but it cannot be denied compound. The wide application of materials in automobiles, especially in the Chinese automotive industry, is still widely used in various aspects of application technology. This requires us to pay attention, research, discussion and practice. This paper discusses four major application technical issues such as painting, connection, maintenance and recycling of automotive composite materials.
Painting of automotive composites
In the automotive industry, the quality of the exterior paint of the car body is one of the most important indicators of the quality of the car, because the car paint surface not only protects the car from corrosion, but also has a very important influence on the car's beautification appearance. Therefore, although the automobile production OEMs recognize that composite materials have various advantages compared with conventional metals, they still retain the same attitude as to whether the surface of the composite material has the same quality as the metal surface. In fact, one of the biggest challenges encountered in the use of composite materials in automotive body panels is the flaws that result from the composite coating.
For example, we use the SMC parts with the most use of composite materials in automotive body panels. SMC body parts usually produce a lot of surface defects after painting, such as: pinholes, pores, cracks, bubbles, etc., especially in the body. The bubble in the edge area of ​​the panel is more serious. In order to make up for these defects, reduce the rate of unqualified products, and improve the surface quality of components, domestic manufacturers are currently improving through a large number of post-painting repair methods such as foam breaking, grinding, filling putty, polishing, etc., and then according to the usual The surface is repainted by the coating process. Although the result of this reduction has reduced the rate of non-conforming products, a large number of post-repair processes and re-coating have increased the production cost, and the application of SMC on the A-class body panels has also been limited.
The majority of the causes of surface paint flaws and blistering of SMC body panels after painting are attributed to tiny pores and microcracks in the matrix. These tiny pores and microcracks are often not artificially formed during production and handling, such as from the molding of parts to the process of demolding to edge removal, and from the packaging of components to the transportation process, we often find that Many microcracks are generated at the edge portion of the component. It is these seemingly insignificant tiny pores and microcracks that accumulate moisture in the air and volatile solvents in the paint during the paint spraying process. When the painted SMC parts are baked at high temperature through the oven, the water and solvent expand and evaporate. The bubble is escaping, causing the surface of the sprayed component to foam or the bubble to break into a paint smear such as a pore or a pinhole.
As for the surface flaws produced by SMC components after painting, the main practice in the foreign composite materials industry is to eliminate micro-pores and micro-cracks, and to eliminate the root causes of paint surface defects from the roots, and have received good results, mainly the following Several measures:
1. Produce high strength, high toughness SMC resin.
In recent years, AOC Corporation of the United States and Thyssenkrupp Budd have jointly developed a new SMC resin from Atryl® TCA. This SMC resin has high strength and produces parts that reduce surface waviness by 50% (compared to conventional SMC surfaces) and increase toughness by 69% (compared to conventional SMC resins). Due to these properties, the generation of microcracks during the demolding process and demolding can be significantly prevented, so that microcracks are not generated even in important edge regions.
2. Strengthen molding process control and mold technology advancement.
By changing the SMC sheet feeding mode and sheet layup position; increasing the material flow distance; making the material evenly displaced during the mold closing process to reduce the porosity of the SMC component. The specific method is to use the PLC and NCN control composite material press to control the molding process of different parts of the product molding process; use the laser locator to correctly position the material covering. In addition, vacuum-assisted exhaust dies are used for large or complex parts, and compression molding is performed under vacuum conditions, which can significantly reduce or even eliminate SMC porosity defects.
3. Develop new primer coatings and new coating processes.
In 2003, BASF launched the DynaSealTM UV-curing sealing agent for the SMC “paint bubble†problem. This technology allows the SMC parts to be sealed by UV-initiated polymerization before the painting is dried. In the curing of the paint, this layer of UV-cured sealing agent prevents the volatiles absorbed in the SMC matrix from escaping, thereby avoiding the generation of pores. Another method is the in-mold coating (IMC). After the SMC is completely cured inside the mold, the operator injects a layer of liquid coating material, which is then cured on the surface of the SMC and filled with all the voids, while providing a primer-like surface that prevents it. The production of paint bubbles. |
4. Civilized production, civilized handling.
The microcracks generated by SMC components are largely due to the process of demolding to edge removal, as well as uncivilized production and uncivilized handling during the packaging and transportation of components. Therefore, it is of vital importance to strengthen the education of civilized production and civilized handling. Foreign countries have generally implemented the "products not to land" civilized production mode, and vigorously promoted the special-purpose turnover box (frame) logistics form in the automotive composite materials industry, reducing the number of handling, Do not let the parts collide with each other to prevent micro cracks caused by human factors.
The above-mentioned several new foreign materials, new processes and new technologies focus on solving the unsatisfactory defects of automotive composite materials in terms of coating, eliminating the obstacles that limit the large-scale application of composite materials, enabling composite body panels to reach or The level of paint that exceeds the traditional steel materials, so that the application of automotive composites will become increasingly widespread.
Automotive composite connection and fixing
With the increasing application of automotive composite materials, the combination of automotive composite parts and the connection of composite parts to adjacent metal parts has become increasingly prominent. The connection between traditional metal parts in the automotive industry has been unable to adapt. Objectively, in this case, it is necessary for us to learn and recognize the connection and fixed connection of automotive composite materials and make reasonable choices. According to the mature experience of foreign countries, there are three main ways to connect and fix automotive composite materials: (1) mechanical fastening; (2) adhesive bonding; (3) welding/welding.
Mechanical fastening This type of attachment method uses rivets and bolts and is the most popular and easiest to understand connection. For the automotive industry, there are many deficiencies in mechanical fastening methods, such as weight gain, stress concentration, overlap between components, high tolerance requirements, and electrical erosion. However, on the other hand, the mechanical connection does not require surface treatment or subsequent polishing, so repeated disassembly is convenient (eg inspection, repair and recycling). Relatively speaking, the impact on the environment is not very sensitive, such as the impact of temperature.
The adhesive bonding and fixing method has the following advantages as compared with the mechanical fastening and fixing method: the structure weight is reduced, the appearance is smooth and smooth, the fatigue strength is improved, the adaptability is strong, and the connection is thinner for the thin-walled component, and the bonding process is simple. Shorten the production cycle. However, there are some disadvantages in the adhesive bonding and fixing method, such as the working temperature range of other components is not high; the bonding quality is susceptible to different factors, and the dispersion of product performance is large; there is no reliable inspection method; bonding The surface treatment and bonding process are more demanding; special heating and pressure treatment bonding tools are required. Therefore, in some important parts and connection positions, a hybrid connection fixing method of bonding to a certain mechanical fastening connection is often used, which fully utilizes the advantages of bonding and ensures sufficient strength and reliability of the joint portion. .
The welding/welding joint fixing method is mainly applied to thermoplastic automotive composite parts. The main advantages of the welding/welding joint fixing method are: good mechanical properties, durability of joints, short processing time, easy on-line inspection and low surface treatment requirements. Wait. There are three main welding/splicing connection fixing methods that can be used for thermoplastic automotive composites: (1) ultrasonic welding/welding, (2) induction welding/welding (3) resistance welding/welding. Welding/welding of automotive composites has the following disadvantages: it is not easy to disassemble, it needs to add conductive filler (for induction welding/fusion), metal mesh is needed (for resistance welding/fusion), and the allowable carbon fiber content is very high. Low (all three welding/fusion processes), etc.
According to the above brief introduction, we know that there are three main ways to connect and fix automotive composite materials, each with its own advantages and disadvantages, to adapt to different applications. However, relatively speaking, the most promising automotive composite joining process is the use of adhesive bonding and fixing methods. As the binder continues to improve in functionality, it has dual effectiveness (both bonding thermosetting composites and bonding) The development of thermoplastic composites and the direction of environmental protection, the method of connecting and fixing automotive composite adhesives is increasingly valued, accepted and prevalent in the automotive industry. Due to space limitations, the connection and fixing of automotive composite materials in this section mainly discuss adhesive bonding and fixing methods.
Advantages of automotive composite adhesive bonding and fixing method
In recent years, due to the emergence of high-performance structural adhesives, the connection method using adhesive bonding has been continuously recognized. As one of the most promising joint fixing processes, it has many outstanding advantages:
1. The mechanical properties of the adhesive can be determined according to specific design requirements (eg, impact resistance);
2, the adhesive's superior anti-fatigue and corrosion resistance can extend the service life of the product;
3, the adhesive has a good sealing;
4, the two materials or structures bonded together can achieve a relatively smooth surface, with the advantages of design;
5, through the entire bonding area to disperse the load on the component, thereby avoiding the concentration of local maximum pressure;
6. The characteristics of the adhesive filled voids allow the parts to have certain tolerances;
7. Adjust the hardness of the adhesive to optimize the hardness of the entire product.
Types of structural adhesives commonly used in automotive composites
In general, automotive composite structural adhesives generally use three types of adhesives based on epoxy resin, polyurethane resin and acrylate resin. The three types of adhesives also have their own characteristics in use. Different choices for different materials and requirements:
Epoxy Binder: Excellent adhesion to composites, thermosets and metals; high strength, flexibility and elasticity; minimal shrinkage during curing. Divided into single and double components. One-component epoxy adhesives require heat curing and are subject to strict application conditions.
Polyurethane-based adhesive: excellent adhesion to most composite materials and plastics; good adhesion to metal; mechanical properties from rigid to flexible range; long-lasting; but wet during processing Sensitive; a wide range of curing speeds.
Acrylic-based adhesive: excellent adhesion to composite materials and thermosetting plastics; good adhesion to metals; allows poor pre-treatment of adherends; achieves optimal combination of high strength and high toughness; Good chemical resistance, long effective use period; fast curing speed; but bad smell; high shrinkage during curing.
Table 1 shows the typical properties of the three types of structural adhesives for automotive composites. Due to the wide variety of structural adhesives and the requirements for their use, the performance of the structural adhesives should be used. for reference only.
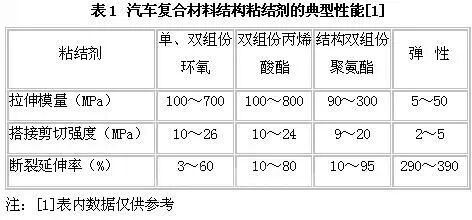
Surface treatment before bonding of automotive composites
Automotive composites (especially thermoplastic automotive composites) have relatively low surface energies, so before using structural adhesives, the surface of automotive composites needs to be properly treated to remove dirt, dust, oil, grease from the surface. , moisture, mold release agent and plasticizer, etc., at the same time, improve the surface energy of the substrate, making it higher than the surface energy of the structural adhesive, thus ensuring that the structural adhesive can fully wet the surface of the substrate, which is achieved Robust, reliable and durable bonding is essential. Below, three common surface treatment methods will be described.
1. Solvent Wiping This is the simplest surface treatment to remove wax, oil and other small molecular weight contaminants from the bonding surface. This technique requires that the contaminant be soluble in the solvent and that the solvent itself does not contain dissolved contaminants. For this reason, the choice of solvent is very important. In general, commonly used solvents include: acetone, methyl ethyl ketone, methyl isobutyl ketone, xylene, trichloroethylene, ethanol and isopropyl alcohol, etc., should be careful to use a clean dust-free cloth or paper towel. However, the disadvantage of this surface treatment method is that the solvent may have an adverse effect on the substrate, such as the thermoplastic composite may be dissolved, showing stress cracks or cracks; it may cause cross-contamination, such as between the sample and the sample. Contamination of contaminated cloth that is contaminated, reused, or immersed in a solvent; steam generated may endanger workers' health; not suitable for large-scale production requirements (large-scale industrial production may use steam degreasing and ultrasonic steam degreasing methods) ).
2. Grinding Method Grinding removes surface contaminants and obtains a highly textured surface that increases the bond interface of the structural bond to create a "bite effect." Commonly used grinding methods include: manual sanding with wire brush, sandpaper or boring; automatic sanding with abrasive belts, grinding wheels or shot blasting/blasting; and relatively fast, low operator dependence and repeatability. Mechanical grinding with good cost and efficiency.
3. Flame Treatment Flame treatment uses a gas or gas/oxygen flame to partially oxidize the surface to create a polar group to increase the surface energy of the polymer. The thickness of the substrate treated by this technique is greater than the thickness of the substrate pre-treated with corona, and is particularly suitable for non-uniform thermoplastic composite articles. The advantages are: the ratio of gas to oxygen, flow rate, exposure time and the distance between the flame and the substrate are easily adjusted, which has proven to be a more efficient method for polypropylene composites.
Surface treatment before bonding of automotive composites In addition to the three commonly used surface treatment methods described above, there are some complex surface treatment techniques that are relatively advanced and quasi-specific bonding requirements, such as plasma treatment corona discharge treatment chemical treatment. Wait. But no matter which surface treatment method is used, the key is to have a clean bonding surface and to ensure that the adhesive can fully wet the substrate, which we should pay close attention to.
Design of automotive composite bonding joints
In addition to the selection and preparation of the adhesive and the bonding surface treatment, the design and bonding of the automotive composite adhesive is a critical step, and the design of the bonded joint will directly affect the bonding performance and strength. The general principle of the design of automotive composite bonded joints is to ensure uniform stress distribution on the bonding surface; to minimize stress, to be purely subjected to tensile and shear forces; to maximize the bonding area. The structural design form of the automotive composite bonding joint is also various. According to the shape of the adherend, it can be divided into a plane lap joint, an angular lap joint, a T-shaped joint and a tube, a rod-shaped joint, etc.; The connection method can be further divided into docking, lapping, docking, pairing double lapping and the like. From the form of the joint, it is generally considered that the plug structure is ideal, followed by lap joint and diagonal lap joint. However, in practical applications, it is mainly determined according to the structure of the bonded product and the portion to be bonded.
The quick stacking door has many functions such as heat preservation and cold preservation, insect and wind prevention, dust insulation and sound insulation. Widely used in underground parking lots, industrial plants, food, textiles, electronics, printing and packaging, automotive assembly, precision machinery, logistics and warehousing and other places.
Automatic Stacking Doors,High Speed Security Door,Rapid Stacking Folding Door,Automatic Stacking PVC Door
Shenzhen Hongfa Automatic Door Co., Ltd. , https://www.highspeedshutterdoor.com