Abstract At the domestic mobile phone product launch conference, we often see such a video: in the workshop where sparks and scraps fly, a steel plate and aluminum plate is slowly sent to the machine tool, fixed four times, so that it can not move, then a metal rod Piercing the steel plate mercilessly at the angle of boring, in the absence of...
At the domestic mobile phone product launch conference, we often see such a video: in the workshop where sparks and steel scraps fly, a steel plate and aluminum plate is slowly sent to the machine tool, fixed four times, so that it can not move, and then a metal rod The angle of the boring drill penetrates the steel plate mercilessly. After a myriad of nine shallow depths, the original rough sheet becomes light and smooth. Then, the 6P lens module of the rear camera is composed of a spring pop-up, and the front and rear panels are highlighted. The Snapdragon 8×0 processor from Qualcomm gives a close-up of the rendering, the angle of the lens is changed, the rhythm of the motion of the picture alternates, and the music is orgasm. When the advent, the various components of the mobile phone will also be merged into one. When Dangdang, a domestic god machine will come. In fact, manufacturers have rendered the mobile phone casing processing technology so dreamy. It is nothing more than to say that our craftsmanship is exquisite and costly. This "universe super dreamy cool CNC 360 degree swivel" processing technology is worth your money. However, in the normal production workshop, there is no photographer who wears Japanese-style warm light, no slap music, some are clunky machine tools, and noisy noise. Under the glare, it is time to restore the real mobile phone casing manufacturing journey.
Full CNC, or die casting? Before restoring this mobile phone casing manufacturing journey, it is necessary to clarify two (three) concepts, the entire CNC process and die casting process, as well as CNC + die casting, the entire CNC mobile phone middle frame is an aluminum plate (or other through the CNC machining center) The metal material is milled into a specific shape. The die casting uses a mold cavity to apply high pressure to the molten metal, and the fluid metal is die-cast into a solid metal casing or a middle frame. Of course, the two processes are combined. Think about it with the tail. I know that the cost of the whole CNC process is relatively high, and the material waste is also more. Of course, the quality of the middle frame or the outer casing under this process is better. The principle of die casting is not waste, saving time and cost, but it is not conducive to the later anodizing process, and may also leave sand hole flow marks and other small problems affecting quality and appearance. Of course, manufacturers have a concept of yield. The reliable manufacturers will not let these defective products flow into the production process behind. After understanding the similarities and differences between the two processes, I began to talk about the metal shell processing technology that has also emerged on the thousand yuan machine. The internal material of the company we got, the mobile phone casing used is the die-casting process. In the die casting stage, before the die casting, we saw the original aluminum. Because the strength and hardness of pure aluminum are not enough, in fact, the aluminum alloy used in the mobile phone has different characteristics depending on the formula. For example, the strength of the 6000 series aluminum alloy used in the iPhone 6 is not enough, but the ductility is better, and it is easy to be bent. The 7000 series used in the iPhone 6s is much stronger, but it is more brittle. It is more difficult to be deformed by pressure, but once it exceeds the load, it is not bent, but broken. Well, according to the manufacturer's demands, the formulation of aluminum alloys is also different. For example, the aluminum below is added with precious metals such as rare earth, titanium and cobalt. Of course, the proportion of these precious metals is very low, and compared with gold and platinum. Real precious metals are actually not that expensive.
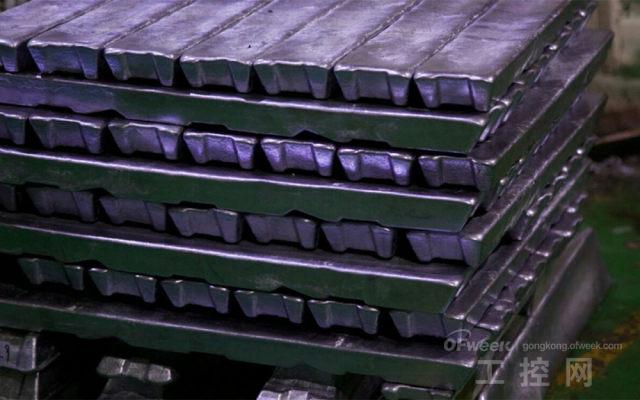
Since it is die-casting, it is impossible to directly take the aluminum material, but it needs to melt the aluminum into a fluid, which is convenient for subsequent stamping and forming in the mold, so the picture below is temperature-bearing.
When these metals become fluid, it is time to inject into the die casting machine, which is the most difficult moment in the life of aluminum. The aluminum water slowly flows down from the spider-like groove, accepts unimaginable punching, and finally becomes a shell. The prototype. Although it seems relatively simple, even in such a link, the shell must be protected from sand holes at all times. Once there is a sand hole, there will be a small pit in the subsequent processing and cutting, so there is still room for improvement. Process and mold structure, this trial and error improvement process will waste a lot of raw materials.
When a piece of aluminum water goes on, after the stamping, the manipulator will peel off the outer shell and send it to the assembly line for the next round of tests.
Painting stage After the end of the previous die-casting stage, these prototypes have to accept the next choice. They are anodized like the iPhone to achieve an icy metal texture, or they are sprayed and put on a warm coat. ? This seems like a difficult decision. But the reality has nothing to do with aesthetics: die-casting is not conducive to anodizing, and there are some product differentiation considerations.
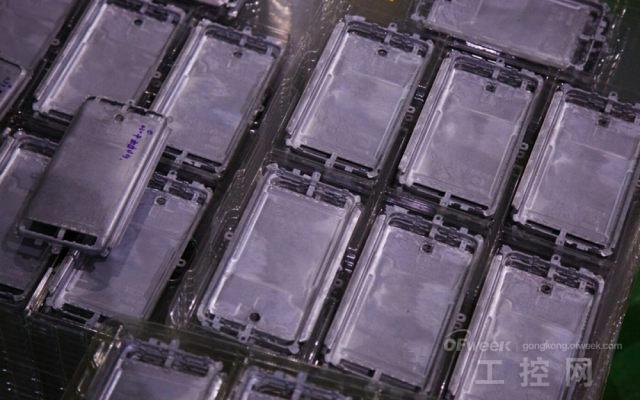
After machining through the machine, the excess is washed away and the burr is worn away. It can be seen that the outer casing has been basically formed. As for the opening above, it is left for injection molding. The small holes on the back cover are CNC machined for injection molding and reinforcement. This logic is the same as the white strip on the back of the iPhone 6. In order to make the antenna signal smooth, the back cover cannot use a complete piece of metal. So in the antenna part, we will always see traces of plastic. There is currently no way to overcome this, and this part of the plastic is not a spray point.
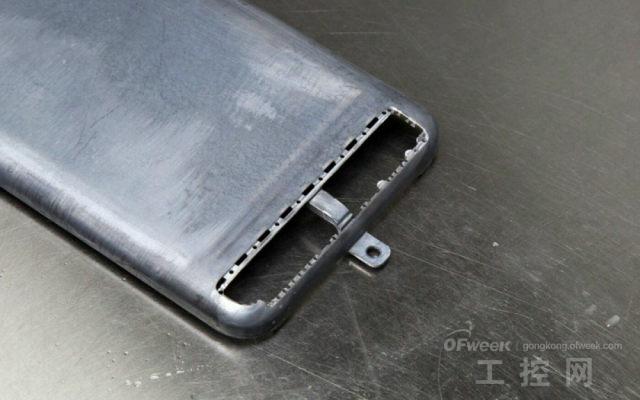
After the injection molding is completed, after re-grinding, the next step is the process of painting. The manufacturers will definitely not take the above-mentioned plain shell directly. The process of painting is actually a technical activity. The mobile phone has a clear dividing line between the plastic and the metal part of the back. If the painting process is not good enough, the dividing line will still be visible, so the boundary between the metal and the plastic cannot be seen. It is an important indicator to judge whether the painting process is good or not. The lower phone case will slowly advance on the assembly line, and 8 groups of 16 nozzles will spray the casing in all directions to ensure uniformity.
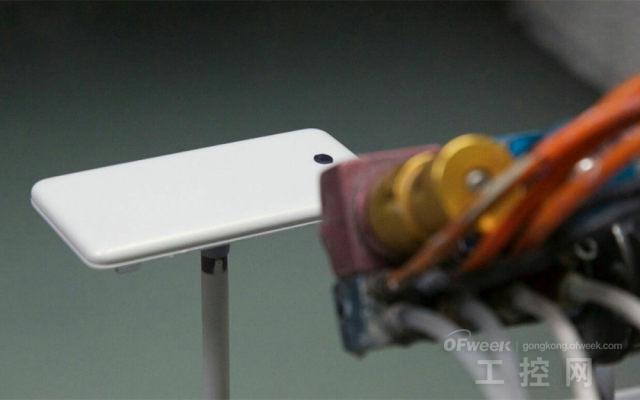
After the painting is finished, it is painted, and the process like the mushroom jungle is the process of baking paint. Moreover, painting and baking varnishes are generally not once, but are repeated several times. And between the paint and the paint, there will be another grinding. This set of mobile phone shells will eventually undergo 5 paintings, 5 paints and 2 times. Usually the first time is the primer, the last time the paint will be added pearl powder or aluminum powder to ensure the texture and look.
The CNC stage has reached this step, which is the favorite part of the mobile phone manufacturers, because this part has a very nice part, called diamond cutting. However, before the diamond is cut, the manufacturers also need to open the camera, volume keys, speakers, etc., and the bottom is to open the camera hole to the shell.
After each hole is opened, it is a diamond cutting link that you like to hear. It is said that the diamond cutting is not because the cut frame is crystal clear like a diamond, but the cutting tool is a diamond.
Below you can see the yellow part in front of the cutting prop, which is the diamond. As for why it is meager compared to the diamond on the diamond ring, I guess it should be synthetic diamond, with the hardness of natural diamond, but without the diamond after cutting. Gloss. It can also be seen below that the edge of the cut case has a good high gloss. It's not quite similar to the previous paint spray. The diamond cut here can't be done again, twice at least, and three times is the conscience of the industry. After all, one more step, it costs more.
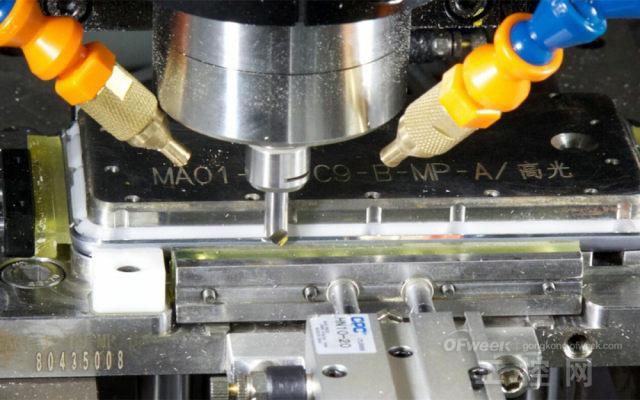
It should be pointed out that in order to ensure that the width and angle of the cutting are strictly consistent, it is necessary to use a kind of laser tool setting instrument to control the thickness of the knife edge and the width of the trimming edge. After all, in this world, The most straightforward is not Wang Lihong, but the light. To put it simply, the laser is used to make a circle in the place to be cut. The data is measured and fed back to the CNC machine according to the shape of the object to be measured, and then the cutting can be started. Ok, here is a close-up of the MVP diamond cutter for this mobile phone case manufacturing tour.
What the manufacturers showed us is a glamorous process, but in the field we found that from an aluminum enamel to a delicate outer shell, the process of going through is quite a bit, and some processes are even cumbersome, but like the girls are willing to look good in the face as Dong Daozi, knife it should be on the housing.
Window Light
It can be installed quickly and easily. You only need to open a 7.5-10cm hole in the ceiling, connect the wires, and then clamp the fixing device to the opening to complete the installation without tedious steps.(Please cut off the power supply before installation for your safet). Great for Showcase, Bedroom, Corridor, Dinning room, Restaurant, Bar, Cafe, Hotel, Bedside, Living room, Stair, Aisle, Balcony, Bathroom, Toilet, Tea room, etc. Jiangmen Synno Co., Ltd is a high and new-tech enterprise. Our company specialized in LED green light source. And we are engaged in medium and high-end LED decorative lighting with a whole set of design and manufacture of lamps and lanterns, development of control system and engineering supporting service. Our company is devoted to provide customers with LED application products. Synno has got through ISO9001 quality system certification of SGS of Switzerland, CE certification of European Union, GS certification, ROHS certification and relevant domestic LED lamps and lanterns certification.
led window lamp, window led lamp, window door lamp, rotatable window light, corridor window light
Jiangmen Synno Lighting Co., Ltd. , https://www.synnoled.com